▍摘要
摘要:G316河谷汉江公路大桥所处水域地质以卵石和致密砂岩为主,介绍采用静压植桩技术结合螺旋钻掘和旋挖钻引孔工艺进行钢板桩施工的工艺和监测,可为类似工程提供参考。
关键词:桥梁基础;静压植桩技术;卵石和致密砂岩;深水钢板桩围堰;围堰监测
▍1概述
近年来,跨河、跨江、跨洋的桥梁建设得到了快速发展,深水基础也随之增多。深水基础以其施工难度大、安全风险高、施工周期长等特点成为大跨度桥梁建设的关键环节。深水基础的施工,直接受水域环境影响,随着水深的增加,未知及可变的自然因素相应增加,桥梁基础的施工难度增加。国内桥梁深水基础较多采用大型群桩基础,随之相应地有多种围堰施工技术,主要形式包括锁扣钢管围堰、双壁钢围堰、钢板桩围堰、钢套箱围堰等。河谷大桥项目采用拉森钢板桩围堰进行主桥承台施工,对传统工艺进行了优化改进,克服了大直径卵石层和致密砂岩中钢板桩围堰的施工难题。
1.1地质水文
(1)地质情况。大桥主墩桥址区岩(土)层自上而下可分为:卵石(Q4al+pl)、强风化细砂岩(E2F)、中风化泥质粉砂岩(E2F),其中卵石最大粒径可达80cm,地质分布情况见表1。
(2)水文情况。桥位所在区域汉江河床宽度为250~400m,最大流速为2.32m/s,最大流量26500m3/s。通过分析地方水文站提供的桥址处过去16年的月最高水位及过去2年的日平均水位,确定钢围堰施工、使用期间主桥桥位处的常水位约为77m。
1.2工程概况
河谷大桥主桥承台尺寸24m(长)×19m(宽)×5.5m(高),采用18m长拉森SP-Ⅵw型钢板桩围堰施工。围堰长28.8m,宽22.8m,围堰外设计水深5.9m,深入河床11.1m,围堰内基坑底至钢板桩顶高12.7m。主墩围堰设计3层围檩支撑,围檩采用2NH700×300型钢,角撑、对撑采用630×10mm钢管,钢板桩材质采用Q295bz,围檩支撑材质采用Q235。设计承台顶标高+72m,承台底标高+66.5m,钢板桩顶标高为+79m,设计最高水位+78m。主桥钢板桩围堰三面均设有钢栈桥,钢栈桥钢管桩距离围堰钢板桩约2.5m。采用振动锤对钢板桩进行试打,钢板桩受到大直径漂石的影响根本无法穿过大直径漂石层。当把局部区域的大直径漂石层清除以后,采用振动锤插打钢板桩入砂岩层最大深度仅为1m左右,不能达到设计要求。经过不断地摸索、实践,最终确定了采用旋挖钻引孔+螺旋钻配合静压植桩机安装钢板桩、无封底施工的施工工艺。围堰结构侧视见图1,钢围堰结构平面见图2。
▍2施工工艺
2.1施工准备
(1)拉森钢板桩进场质量检验后需要进行锁扣通过试验,之后在锁扣内涂抹黄油,主要起锁口润滑及防渗作用。质量检验主要检查项有钢板桩尺寸、变形程度及材质。
(2)全站仪测定围堰周边线,确定围堰位置,旋挖钻承台中心点位置钻孔至承台底标高下4m,埋入型钢立柱并浇筑混凝土,用以支撑围檩对撑,提高围堰整体稳定性。
2.2旋挖钻机引孔
将桩位上方平台面板移除,平台基础钢管上安装双层型钢导向架,吊车安装直径为1.2m的钢护筒,振动锤插打钢护筒至无法下沉,旋挖钻孔至护筒底上方20cm,继续插打钢护筒,反复循环直至护筒穿过大直径卵石层进入下部岩层1m。回填袋装素土至河床标高以上约1m位置,旋挖钻将钢护筒内的袋装素土夯实。引孔后回填要确保密实度,回填时利用编制袋装好素土,每个编织袋只装入约60%的素土,防止装入过多导致间隙过大、出现不密实的情况,然后向护筒内抛入装好素土的编织袋,每回填1m高度后采用旋挖钻钻头向素土施压,降低回填土间的间隙。一次施工6根钢护筒,回填完毕后振动锤拔出钢护筒依次循环施工。
2.3钢板桩植入
(1)静压植桩机的工艺机理与各类传统的打桩机不同,它是采用通过夹住数根已经压入地面完成的桩,将其拔出阻力作为反力,利用静荷载将下一根桩压入地面的体系结构。压入中利用“除芯理论”钻掘压入桩桩端正下方的地基,用与压入桩同时被夹持的螺旋钻,钻掘钢板桩端正下方后,将螺旋钻拔出一定距高,使局部产生间隙时,压入钢板桩,见图3。采用压入机理进行钢板桩压入施工时,桩端附近土体会因为压实变硬形成一个压缩区域,称为“压力球根”。因为有“压力球根”的存在,给桩基结构提供水平和垂直方向的强度,从而保证了钢板桩围堰的结构稳定性。
(2)前5片钢板桩在平台上植桩,预先将钢板桩接长6m,植桩机在平台上拼装就位。吊车吊装钢板桩就位,钢板桩下口与螺旋钻套管底部焊接固定,钻掘至设计桩底标高以上0.2m,吊车将螺旋钻向上拔同时植桩机夹住钢板桩向下静压,使螺旋钻与钢板桩脱离,压入钢板桩至设计标高,依次循环完成前5片钢板桩,割除钢板桩顶部6m至设计顶标高,前5片钢板桩即可作为植桩机施工作业平台,将植桩机在已施工的钢板桩上进行固定。钢板桩下口与螺旋钻套管底部焊接固定主要目的是为防止螺旋钻杆夹头开启状态下钢板桩自重导致下落,同时也防止从钢板桩前端土压引起螺旋钻与钢板桩前端部脱离,当钢板桩进入岩层达到底标高后通过螺旋钻杆反向转力可使钢板桩与螺旋钻杆焊接处脱焊,最后拨出螺旋钻杆。注意精确控制钢板桩长度,每一根钢板桩植入前都需要精确量测长度,当钢板桩植入到位后通过钢板桩顶标高减去钢板桩长度来复核钢板桩底是否达到设计标高。
(3)在钢板桩围堰四周平台的钢管柱上焊接垂直于钢板桩墙的I36b主支撑工字钢,在主支撑工字钢端头再焊接梳齿形状的12.5H型钢支撑,顶在钢板桩上,防止钢板桩倾斜。该支撑装置有效提高了钢板桩自由端刚度,提高了静压植桩机的稳定性,保证了植桩机的施工安全。通过在钢板桩围堰角点安装镭射装置对钢板桩安装进行定位导向,从而控制钢板桩轴线偏位,钢板桩整体线型得到有效保障。植桩机每植桩1根后行走至下一片钢板桩位置,施工至角点位置时调整植桩机角度向外,角点外50cm处植入1根辅助桩,调整植桩机角度向内,植入角点后2根钢板桩。
(4)将植桩机主体起吊转向后固定、拼装再继续施工,当所处岩层强度较大,无法带桩植入时,先采用大钻头引孔,再带桩植入,采用定位系统控制平面位置,电子水平尺检测钢板桩垂直度。施工至合龙口时,先测量合龙口的形状,确定合龙桩的尺寸现场加工成型,完成合龙桩植桩。
2.4围檩及内支撑安装
(1)本项目钢板桩围堰共设计3层内支撑,第一层内支撑在钢板桩合龙后即开始施工,在钢板桩上围檩底标高的下部安装牛腿用于支撑围檩,围檩安装好后在外侧钢板桩与围檩之间焊接一块定尺型钢使外侧钢板桩与围檩顶紧。
(2)在栈桥上预先制作好角撑,法兰螺栓连接牢固,角撑两端焊接三角型钢垫箱,吊车整体下放至第一层围檩位置,钢垫箱与围檩焊接牢固并焊接加劲板。内支撑的安装时考虑平衡受力,先安装中间支撑,对称安装四周的斜撑。对撑分2节用吊车下放安装,安装第一节时先一端与围檩焊接牢固,另一端担在中心HN400型钢立柱上,再吊装第二节对撑,安装与第一节对撑连接部位,另一端与围檩加塞钢板焊接牢固,在栈桥上制作好小角撑,一端焊接钢垫箱,吊车逐个安装。干挖基坑至第2层内支撑下方0.5m,安装第2层围檩及内支撑。继续开挖基坑至第3层内支撑下方0.5m,安装第3层围檩及内支撑。随着基坑开挖的深入,围堰内外压力差递增,导致内支撑轴力增大有一定压缩,内支撑螺栓会松,需要及时安排人员紧固,防止下挠引起的剪断失稳,致使钢围堰失稳。
河谷大桥24#围堰
2.5基坑开挖
开挖大直径漂石层时,采用挖掘机直接开挖,采用2台小型挖机、1台长臂挖机及1台25t汽车吊,长臂挖机将基坑内的漂石挖出,长臂挖机够不着及钢板桩附近的区域采用2台小型挖掘机进行开挖,小挖掘机挖出的漂石可以转运至长臂挖机可覆盖的区域,通过长臂挖机将其挖出,也可以装入渣料斗通过吊车吊出基坑。开挖致密砂岩层时,由于部分区域砂岩层强度高,挖掘机无法直接开挖,因此需要在围堰内配备1台带炮锤的挖掘机,通过炮锤对坚硬的砂岩层进行破碎,然后再通过挖掘机、吊车将开挖后的砂岩运出基坑。开挖至承台底下方0.2m后清理桩头,并拆除所有护筒。设置盲沟集水井,通过观察发现基底部渗水量较少,因此仅浇筑0.2m厚混凝土垫层即可。
2.6围堰堵漏
钢围堰施工完成后,观察现场基坑底的渗水情况后,发现基底的渗水情况并不严重,采用2台水泵抽水,未对钢板桩的入土范围内的地层进行注浆止水处理。钢围堰施工完成后发现在局部的钢板桩锁扣处有漏水现象,将中粗砂在围堰外靠近钢板桩锁口位置向下撒布,利用内外压差将砂吸进漏水的钢板桩锁口缝隙中,并配合薄膜塞缝进行堵漏。通过现场实施,堵漏效果很好,采用上述方法封堵之后,钢板桩之间不再有肉眼可见的漏水点存在。
面对河床以下局部钢板桩锁扣处涌水,设计了一种U型钢板配合活动螺杆将加塞钢板、止水带拧紧至锁扣处的方法进行止水,见图4。在2根钢板桩锁扣漏水处焊接1块“U型钢板”(类似于槽钢形状),U型钢板宽0.2m,钢板厚0.01m,将U型钢板焊接至锁扣涌水处,在U型钢板背面钻1个0.03m直径的螺杆孔,螺杆眼中心对准锁扣漏水处,螺杆孔两侧分别布设螺栓,将螺杆穿入孔中,再准备1块宽度0.16m、厚度为0.01m的钢板和1条0.06m厚止水带,将止水带紧贴钢板桩锁扣处,再将钢板贴在止水带上,最后通过人工拧入螺杆顶压钢板,操作中务必使螺杆紧紧顶住钢板,此时,通过螺杆拧入压力使钢板、止水带紧紧挤压在锁扣处,从而阻止了外部的涌水。
河谷大桥23#围堰
2.7钢板桩围堰体系转换
(1)承台第一层混凝土浇筑完成后,需要拆除影响墩身施工的第三层内支撑。将承台与钢板桩间回填砂土,由于钢板桩围堰内支撑较多,且钢板桩与承台间隙小,砂土回填采用长臂挖掘机回填。砂土回填顶标高距离第一层承台顶50cm,再浇筑50cm厚混凝土圈梁,待混凝土强度达到85%后拆除第三层围檩及内支撑,内支撑拆除时考虑平衡受力,对称拆除。
(2)第二层承台浇筑完成后,继续回填砂土,回填砂土顶标高距离第二层承台顶50cm,再浇筑50cm厚混凝土圈梁,待混凝土强度达到85%后对称拆除围檩及内支撑。
(3)当墩身施工出水面,围堰内回水,保证内外水压差相同,拆除第一层围檩及内支撑,体系转换完成,最后拔出钢板桩。内支撑体系转换示意见图5。
▍3围堰监测
钢板桩围堰主要受力由钢板桩及内支撑承担,本桥围堰高度较大,设计水位至基坑底高差达11.5m。随着围堰逐层向下施工,围堰内外水位高差增大,如果钢板桩及内支撑的应力超过材料最大容许应力,就会造成结构破坏、围堰坍塌。虽然结构设计及验算满足要求,但实际施工与理论计算不可能完全一致,因此需要对围堰进行实时动态监测,及时掌握钢板桩围堰的变形和受力情况,对可能出现的险情及事故提前预警,必要时停止施工、分析原因并采取必要的技术措施确保施工安全。
对围堰进行应力和变形监测,主要监测内容包括:桩顶水平垂直位移、桩身变形、桩身应力、支撑轴力。
3.1桩顶水平、垂直位移监测
在钢板桩顶,在围堰每边的1/4、1/2、3/4位置各布置1个监测点,总计12个监测点。采用棱镜加长连接杆将莱卡GPR1棱镜牢固焊接在钢板桩顶部。采用莱卡TS09plus全站仪测量监测点到测站的距离和夹角,计算监测点的坐标。通过坐标变化量来反映监测点的位移量。每次测量后根据监测点的位移值绘制桩顶水平、垂直位移曲线。
3.2桩身变形监测
矩形钢板桩围堰的四边中间位置变形较大,故桩身变形监测点分别布设在围堰各边中点,埋设深度跟钢板桩长度相同。钢板桩插打前,在钢板桩凹槽内安装一根通长的圆钢管并与钢板桩满焊牢固,将圆钢管的下口用钢板焊死,随钢板桩一起植入。将测斜管安装入圆钢管内,深度达到钢板桩底位置,安装时测斜管口安装保护套,最后用细砂将圆钢管与测斜管之间的空隙全部填充密实,使测斜管牢固固定在圆钢管内。采用XHY-CXxx滑动式测斜仪进行监测,测斜管安装完成后,将测斜仪探头下放到孔底,向上每隔50cm采集1次。初次采集为初始值,初始值连续测定2次,取稳定平均值作为初始值,每次监测后绘制测斜曲线。
3.3桩身应力监测
矩形钢板桩围堰的四边中间位置受力较大,故在围堰每边中点位置设置4个检测断面,根据6个工况的受力结果在每个断面布置3个测点,3个测点分别布置在第一道支撑与第二道支撑中间、第二道支撑与第三道支撑中间、第三道支撑与基坑底中间。将钢表面应力计焊在钢板桩指定位置并将线缆引出至智能监测平台,由智能监测平台定时读取数据,根据每次收集数据计算单次变形量和累计变形量,并结合工况绘制桩身应力时程曲线。在围堰内抽水前3d测取稳定数值当作基准值,围堰内抽水时开始进行监测。
3.4支撑轴力监测
根据《建筑基坑工程监测技术规范》(GB50497-2009)中相关要求,钢支撑的监测截面宜布置在支撑长度的1/3位置或端头,本项目在每根支撑的1/3位置安装钢表面应力计,共设置15个测点,每层5个。每层钢支撑安装前将钢表面应力计焊接在支撑杆件上,与支撑一同安装并将线缆引出至智能监测平台。由智能监测平台定时读取数据,根据每次收集数据换算成支撑应力,再计算出支撑轴力变化值及累计轴力变化值,结合工况绘制轴力时程曲线。
3.5监测频率
主桥钢板桩围堰施工监测项目及监测频率见表2。
3.6监测预警
监测预警值设置主要依据分别为:钢板桩和内支撑有限元计算结果、《建筑基坑工程监测技术规范》(GB50497-2009)中基坑及支护结构监测报警值表,按照一级基坑报警值(绝对值)设置,监测预警值见表3。
3.7智能监测平台
本项目围堰监测采用集成监控平台,可实现桩身应力、支撑轴力的实时测量,可直观对比分析围堰及支撑结构受力变化情况。具有测量精度高、抗干扰力强、可靠性好、操作方便等优点,可实现全天候围堰监测。同时根据预设的预警值,系统在某一项监测项目临近预警值时自动预警,给现场预留充分的应急处理时间,最大程度确保围堰施工人员安全。
▍4工艺总结
4.1优点
(1)采用旋挖钻引孔+螺旋钻配合静压植桩机植入钢板桩施工时,引孔只需穿过卵石层即可,能够克服坚硬地质、大直径漂石以及卵石层地质,避免钢板桩底部砂岩层被破环,确保了钢围堰结构稳定性。
(2)适应各种复杂的自然条件,钢板桩施工效果好,止水挡土效果极佳。螺旋钻钻孔0.7m左右即静压钢板桩跟进,无坍孔风险,回转钻头提钻杆时砂土自动回填、水下密实,可保证封水效果。实践证明开挖后基本无基底涌水,无需浇筑封底混凝土,节约施工成本。
(3)螺旋钻配合静压植桩机植入钢板桩工艺使用旋转前端装有钻齿的桩,切削贯通地下障碍物进行压入,该工法除具有压入原理的无振动、无噪音等施工优点之外,通过使用桩端的特殊钻齿,实现了最小限度的切削,有效地控制了排土量,将对环境的影响控制在最小范围。在实现了环保施工的同时还抑制了桩的偏心和变形,能够高精度地完成植桩。
(4)静压植桩技术能够适用于多种不同的地质和环境条件,本身具备体型小、易于施工狭窄地段的优点。无论是在环境管制严格的区域还是夜间施工,施工都不会受到时间段的限制。
(5)围堰施工质量好,施工完成后通过采用吊铅锤的方法(电子水平尺复核)测得4个钢板桩的最大倾斜率为0.8%,小于规范规定的1%,钢板桩施工质量得到有效保障。
(6)采用3道水平围檩加内支撑的形式,形成稳定的平面桁架,通过在内支撑(斜撑)与围檩之间设置三角形钢垫箱,钢垫箱提前加工预制,提升内支撑与围檩之间的连接质量,内支撑钢管现场采用法兰对接,全装配式构件可在栈桥上先行加工拼装,有效减少了支撑结构的焊缝数量,更加利于围堰施工质量控制,同时极大地缩短了工期。
(7)通过采用智能监控系统对钢板桩围堰全生命周期进行监测,可实现桩身应力、支撑轴力的实时测量,可直观对比分析围堰及支撑结构受力变化情况。具有测量精度高、抗干扰力强、可靠性好、操作方便等优点,可实现全天候围堰监测。同时根据预设的预警值,系统在某一项监测项目临近预警值时自动预警,给现场预留充分的应急处理时间,最大程度确保围堰施工人员安全。
4.2缺点
(1)钢板桩静压植桩机目前只有日本有生产,采购费用非常高。钢板桩静压植桩机施工过程中需要吊车配合打桩,租赁吊车导致施工费用增加。
(2)因为静压植桩机属于特种机械,目前中国国内尚无相应的零配件生产商,完全依赖从日本进口,一旦钢板桩静压植桩机出现损坏,需要更换配件,维修的周期就比较长,很可能会严重耽误工期。
(3)应用智能监控系统对钢板桩围堰全生命周期进行监测尚在初级阶段,还不能做到平台内直接将应变计读数换算成轴力或应力值,还需人工手算且换算工作总量较大。
▍5 结语
本项目深水钢板桩围堰通过旋挖引孔穿过卵石层后钢护筒跟进,然后采用螺旋钻掘和压入联动的“除芯理论”植入钢板桩,成功解决了大直径漂石、卵石层和致密砂岩层地质钢板桩插打难题,围堰植桩完成后其平面位置、标高控制效果好,开挖支撑后无管涌和基底渗水情况发生,因此采取了不封底施工。采用填砂堵漏、薄膜塞缝、螺杆桩止水结合的方式进行围堰堵漏效果较好。本项目围堰施工已顺利完成,围堰监控结果显示,钢板桩的应力、变形、位移均在设计及规范要求的范围内,本项目施工工艺可供大直径卵石层和致密砂岩地质施工参考。
来源:《公路》
作者:母旭彪
编辑:项敏
如涉侵权,请回复公众号
/ 扩展阅读 /
上海喆轩商贸有限公司
广东喆轩实业有限公司
拉森钢板桩销售、租赁
静压植入工法施工
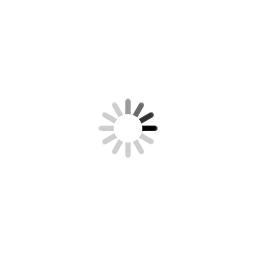
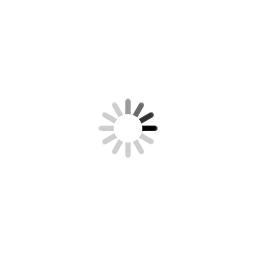
设备、材料仓库分部
上海、南京、南昌、南通、珠海、湛江
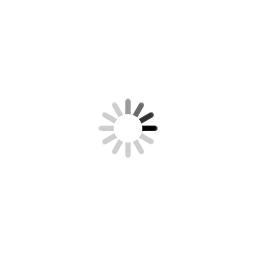
138 1818 6389
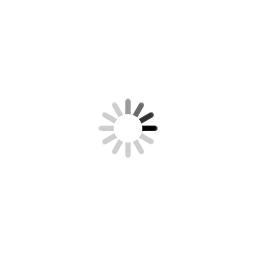
项敏de微信
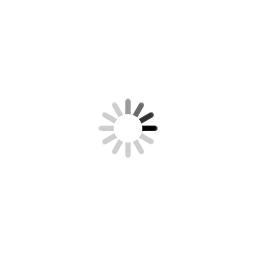
长按下方二维码
关注本公众号:拉森钢板桩
网址:www.lsgbz.com