▍摘 要
摘要:以宁波市地铁5号线C号出入口软土深基坑工程施工为例,介绍了深基坑施工期间对邻近原位大直径原水管的保护措施。通过采用MJS工法加固、TRD工法连续墙围护、坑内高压旋喷桩加固、伺服式钢支撑、科学的开挖方法等综合法施工技术,在保证基坑安全开挖施工的基础上,有效地保护了邻近的原位大直径原水管,相关经验可供类似工程参考。
▍引 言
随着国家经济建设的发展,轨道交通深基坑工程越来越多、环境保护也越来越严格,其中涉及部分地下管线无法迁移而需要原位保护的问题。管线的原位保护要求十分严格。紧邻地铁深基坑的地下管线原位保护技术,除了深基坑的支护结构应安全合理设置外,原位保护的地下管线处软土地基应选择合理可行的加固处理技术,以确保深基坑开挖施工时原位管线的位移变形处于可控的安全范围。曹卫华《MJS工法桩在紧邻保护性建筑物的基坑施工中应用》叙述了基坑应用MJS工法桩+钻孔灌注桩结合1道钢管支撑作为支护结构,成功地保护了邻近的既有建筑,但该基坑挖深较浅,不足6m。董锋《紧邻地下管线的地下连续墙施工预处理技术》叙述了紧邻深基坑围护地下连续墙的原位雨水管道保护,近管道侧槽壁采用高压旋喷桩加固,成功地保护了地下连续墙成槽施工时的原位雨水管道,但该地下连续墙成槽时有泥浆护壁。韩会山《MJS工法在管线保护中的应用》叙述了隧道明挖段紧邻围护地下连续墙的2根合流管线原位保护,应用MJS工法桩加固管线下地基土保护成功,但该地下连续墙成槽时同样有泥浆护壁。本文叙述的地铁软土深基坑挖深达12.5 m,紧邻的DN1600原水管距离基坑等厚度水泥土地下连续墙(TRD工法)仅4.5 m,输水的工作压力为1 MPa,管线采用钢铁管材焊接式接头,容易受基坑开挖影响而位移变形甚至产生裂缝。故如何对大直径原水管线进行原位保护,成为本基坑施工的核心技术问题。本文通过工程实例说明,采用MJS工法桩加固等综合法施工技术及其关键创新点。
▍1 工程概况和地质条件
1.1 工程概况
宁波市轨道交通5号线C号出入口工程,基坑平面形状呈L形,长36.2 m,宽20.5 m,深9.2~12.5 m。基坑围护采用厚850 mm的TRD工法结合3道水平支撑,其中第1道为钢筋混凝土支撑,第2、第3道为φ609 mm×16 mm钢管支撑结合双拼H400型钢围檩。周边重点保护对象为与基坑南侧长边平行的DN1 600原水管,该原水管因供水单位多、居民用水众多而无法停水迁移。原水管采用钢铁管焊接式接头,输水工作压力为1 MPa,横向距离基坑围护TRD型钢水泥土连续墙仅4.5 m(图1)。
1.2 工程地质条件
本工程施工深度范围内的土层从上至下依次为①1a杂填土、①2黏土、①3b淤泥质黏土、②2b淤泥质黏土、③1b粉砂、③2粉质黏土,基坑底处于②2b层中。
场地浅部地下水为孔隙潜水,水量贫乏;③1b层为微承压含水层,水量不大,属疏干型含水层。
▍2 工程难点分析及对策措施
本基坑工程属于软土地基区域,最大开挖深度为12.5 m,坑底大部分处于②2b层,最大的难点是紧邻基坑的DN1600原水管线需要原位保护,且由于先期地铁主体车站基坑(最大开挖深度18.3 m,距离原水管25.1 m)施工,已经造成该原水管位移变形,最大累计沉降量为141 mm,故C号出入口基坑施工更应重点保护。
经综合研判,相应的对策如下:
1)采用MJS工法桩加固DN1 600原水管底的地基土,且在MJS工法桩施工完成后方可施工邻接的C号出入口基坑围护桩及地基加固桩。MJS工法桩机设置有排浆排气装置,故而加固土体时无挤土效应。
2)除基坑的基本监测外,在DN1600原水管顶设置位移变形监测点间距4000 mm,自始至终加强监测,C号出入口基坑施工引起原水管的水平位移累计值不超过10mm,日变形速率不大于1 mm/d。
3)C号出入口基坑采用TRD工法(插型钢)结合3道支撑支护,其中南侧TRD工法中的型钢不拔除,即永久性保留。
4)C号出入口坑内采用高压旋喷桩满堂格栅式加固,加固深度为坑底下4m。
5)C号出入口基坑分层挖土和设置钢管支撑含伺服系统严格按设计施工,钢支撑的安装与预应力的施加必须在12 h内完成,科学利用时空效应。
▍3 施工工艺流程
施工全方位高压喷射注浆(MJS)工法桩→施工TRD→施工坑内高压旋喷桩→第1层挖土→施工冠梁和混凝土支撑→第2层挖土→施工型钢围檩和钢管支撑→第3层挖土→施工底道型钢围檩和钢管支撑→挖土至坑底设计标高→浇筑加强式混凝土垫层→顺作式施工主体结构→分道拆除钢围檩支撑→施工顶板及回填覆土→拆除顶道混凝土支撑→拔除TRD的型钢(南侧不拔)
▍4 关键施工技术
4.1 施工MJS工法桩
采用MJS工法施工形成高压旋喷桩的最大优点是无挤土效应,即环境保护性能好,施工中和土体加固后可有效保护DN1600的原水管。
4.1.1 MJS工法桩概况
M J S工法桩为φ3200mm(摆喷为半圆形平面)@3000 mm,即搭接200mm;加固深度为原水管底以下12m范围,水泥土加固体的28d强度≥1.0 MPa,采用跳桩法施工,且施工间隔时间不小于24h,以防止强制排泥装置将相邻桩体中尚未凝固的水泥土吸入排浆管。
4.1.2 MJS工法桩施工工艺流程
测量放线定桩位→挖基槽坑局部露出原水管→检查原水管顶的位移变形监测管→引孔→MJS钻机设备就位→逐节下放钻杆到设计标高→中压试喷水→边高压喷射水泥浆边强制排泥排气边提拔钻杆→封闭回填基槽坑
4.1.3 MJS工法桩施工参数
M J S工法桩施工参数为:水泥掺量不小于4 0%,每立方米桩中的水泥掺量不小于720 k g;水灰比1.0;水泥浆压力40 MPa;水泥浆浆液流量90 L/m in;主空气压力0.7 MPa;主空气流量1.0~2.0 m 3/m in;倒吸水压力0~20 MPa;倒吸水流量0~60 L/min;削孔水压力10~30 MPa;成桩角度误差控制≤1/100;提升速度20~40 min/m;步距行程25 mm;步距提升时间60、30 s;转速4 r/min;地内压力0.1~0.3 MPa。
4.1.4引孔
引孔采用MDL-135型钻机,配备三叶式钻头及金刚石钻尖,以破除地下障碍物。引孔桩位于原水管外侧100 mm,控制成孔中心与桩位中心偏差小于50 mm,孔深大于设计要求1 m,垂直度偏差小于1/100。插入引孔钻杆如图2所示。
4.1.5 MJS喷射水泥浆
将钻杆(底节钻杆含钻头)逐节下放至引好孔的设计深度;开启倒吸水流和倒吸空气,打开排泥阀门,开启高压注浆泵和空压机;先压力旋喷水流,再切换成旋喷水泥浆;边提升钻杆边继续旋喷水泥浆,拆卸钻杆时,MJS工法桩搭接长度不小于100 mm;最终旋喷水泥浆至原水管底,并持续1~2 min,使浆液涌至原水管中心标高,即超标高喷射水泥浆。施工中实时监控地内压力,并通过调节回流泥浆和气及排浆阀门大小,控制地内压力系数为1.3左右。
4.2 施工TRD
4.2.1 基坑支护TRD概况
TRD通过桩机链状刀具的转动和横向移动,对地基土进行渠式切割与搅拌,并与注入的水泥浆液混合且插入型钢,形成型钢水泥土地下连续墙,兼有支护桩和截水帷幕的功能。本基坑TRD厚850 mm,型钢为H700 mm×300 mm×13 mm×24 mm@800~1 000 mm,型钢长14.6~
33.3 m。
4.2.2 TRD施工工艺流程
测量放线→修挖导向槽→挖预埋穴→安装切割刀具箱→桩机安装就位连接刀具箱→安装测斜仪→边切割边喷浆边搅拌→插入型钢→拔出切割刀具箱→桩机退场养护
4.2.3 施工TRD
工艺参数:采用P·O 42.5水泥的掺量为25%,水灰比1.5。切割液采用钠基膨润土拌制,每立方米被搅土体掺入100 kg膨润土。采用三步施工法——通过注切割液切割、搅拌、注水泥浆混合,主机经往、返、往三步式完成TRD,步进距离控制在50 mm。TRD应连续施工,当天成形墙体应搭接已成形墙体300~500 mm,以保证墙体的防渗性能。拔出TRD切割刀具箱时不应使孔内产生负压而造成周边地面土体沉降。TRD的28d强度≥1.0 MPa。
4.2.4 插入型钢
控制在水泥土连续墙完成后30 min内插入型钢,型钢先依靠自重插入,当插入至连续墙深部时采用振动锤下沉,以保证型钢垂直度不大于1/300。南侧邻近原水管区域的型钢永久保留,其余部位采用专用的液压千斤顶起拔机静力拔除。
4.3 基坑开挖与钢支撑安装
4.3.1 基坑被动区采用格栅式高压旋喷桩加固
应在TRD工法连续墙完成后施工高压旋喷桩。旋喷桩水泥掺量坑底以下为25%,坑底以上为10%,水灰比1.0,喷浆压力不大于20 MPa,钻杆旋喷提升的速度不超过30 cm/min。
4.3.2 基坑开挖
遵循“先撑后挖、限时设撑、分层开挖、严禁超挖”的开挖原则。原水管及其周围5 m范围不得有地面上的施工荷载,只作人行道路使用;其他区域坑边2 m内不得有地面施工荷载,2 m范围外不得超过20kPa。施工首道混凝土支撑和压顶围梁时,采用槽式开挖留设中心岛。
4.3.3 安装钢管支撑及伺服系统
钢管支撑φ609 mm×16 mm按不同挖深分别为1~2道,围檩为双拼H400型钢,支承围檩及钢管支撑的钢牛腿间隔式焊于TRD的型钢内侧。钢管支撑的安装和预应力的施加限时12h完成。钢管支撑伺服系统即自动补偿系统,包括总控制柜、液压泵站、补偿节。采取全天候不间断实时监测钢支撑的受力状态。当钢支撑轴力低于设定值时,系统自动启动进行轴力补偿;当钢支撑轴力超出设定值时,系统报警并根据指令自动调整。即系统根据高精度传感器所测参数值对支撑轴力进行适时的自动补偿来达到控制基坑变形的目的。本工程伺服系统(液压式)设置于钢管支撑的一端,并按照钢支撑预加轴力控制值初步施加预应力,以控制各工况的钢管支撑轴力(图3)。轴力下限值不低于设计轴力的30%,上限值不大于设计轴力,本基坑施工结果均在允许区间内,即累计水平位移不超过20 mm。
4.3.4 施工坑底加强的混凝土垫层
基坑分段分层开挖到坑底设计标高后,限时4h完成加厚为300 mm的C30混凝土垫层,并紧靠TRD。
4.4 支撑的拆撑施工与围护墙中型钢拔除
4.4.1 拆除第3道钢支撑
由于出入口地下结构的侧墙紧贴围护的TRD,即侧墙的外侧利用TRD作为胎模,故底板混凝土施工达到设计强度后,即可拆除第3道钢支撑,施工侧墙和防水层。
4.4.2 拆除第2道钢支撑
由于地下结构的层高较大,最大达9.76 m,即顶板位于第2道钢支撑的上面,故在拆除第2道钢支撑前采用φ609 mm×16 mm钢管换撑,换撑钢管两端焊于地下结构侧墙的预埋钢板,然后拆除第2道钢支撑,继续施工侧墙和防水层。
4.4.3 拆除第1道混凝土支撑
顶板混凝土施工达到设计强度后,施工全外包防水层并回填覆土,拆除第1道钢筋混凝土支撑,恢复市政道路基层及路面,同时拆除换撑的钢管。
4.4.4 拔除TRD中型钢
基坑南侧TRD中型钢不拔除,以避免扰动原水管周围土体影响其安全;其余侧TRD中型钢采用专用的液压千斤顶起拔机静力拔除,拔出型钢后立即采用8%的水泥浆液填充密实。
▍5 结 语
本基坑施工采用MJS工法、TRD工法、科学的开挖及支撑(钢支撑伺服系统)施工技术,严格掌控施工工艺流程和各项施工工艺参数,其中控制地内压力是MJS工法施工的关键技术。在MJS工法桩和TRD的质量达到设计要求的基础上,进行科学合理的基坑挖土及钢支撑安装,以及各根钢支撑伺服系统的自控应用,从而保证了基坑安全有序施工和原水管的安全有效供水,使综合式原水管的保护技术获得成功。基坑监测和原水管顶位移变形监测均符合设计要求,本基坑监测结果表明,基坑水平位移累计值最大为19mm,日变形速率最大为2mm/d,均未超过设计要求的限值。其中靠近原水管侧的水平位移累计值为9mm,原水管顶位移累计值8mm,均小于设计要求的限值10mm;受到地铁建设单位好评。本施工技术可供类似基坑工程施工参考。
来源:《地基基础》
作者:张文华
编辑整理:项敏
如涉侵权,请回复公众号
138 1818 6389
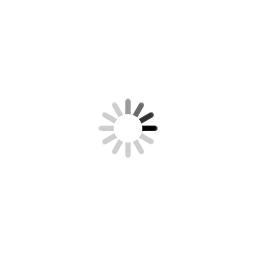
▍TRD工法
TRD工法(Trench-Cutting & Re-mixing Deep Wall Method),又称等厚度水泥土地下连续墙工法,其基本原理是利用链锯式刀具箱竖直插入地层中,然后作水平横向运动,同时由链条带动刀具作上下的回转运动,搅拌混合原土并灌入水泥浆,形成一定强度和厚度的墙。
TRD工法通过水平横向运动成墙,可形成没有接口的等厚连续墙体,其止水防渗效果远远优于柱列式地下连续墙和柱列式搅拌桩加固,其主要特点是环境污染小、成墙连续、表面平整、厚度一致、墙体均匀性好、防渗性能好、施工安全,与传统柱列式地下连续墙相比隔渗,经济性好。
TRD工法适应粘性土、砂土、砂砾及砾石层等地层,在标贯击数达50~60击的密实砂层、无侧限抗压强度不大于5MPa的软岩中也具有良好的适用性。可广泛应用于超深隔水帷幕、型钢水泥土搅拌墙、地墙槽壁加固等领域。
TRD工法动画演示
TRD工法施工流程及典型案例
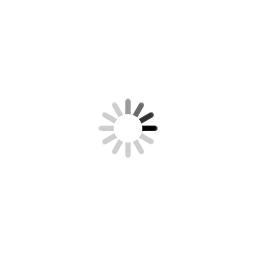